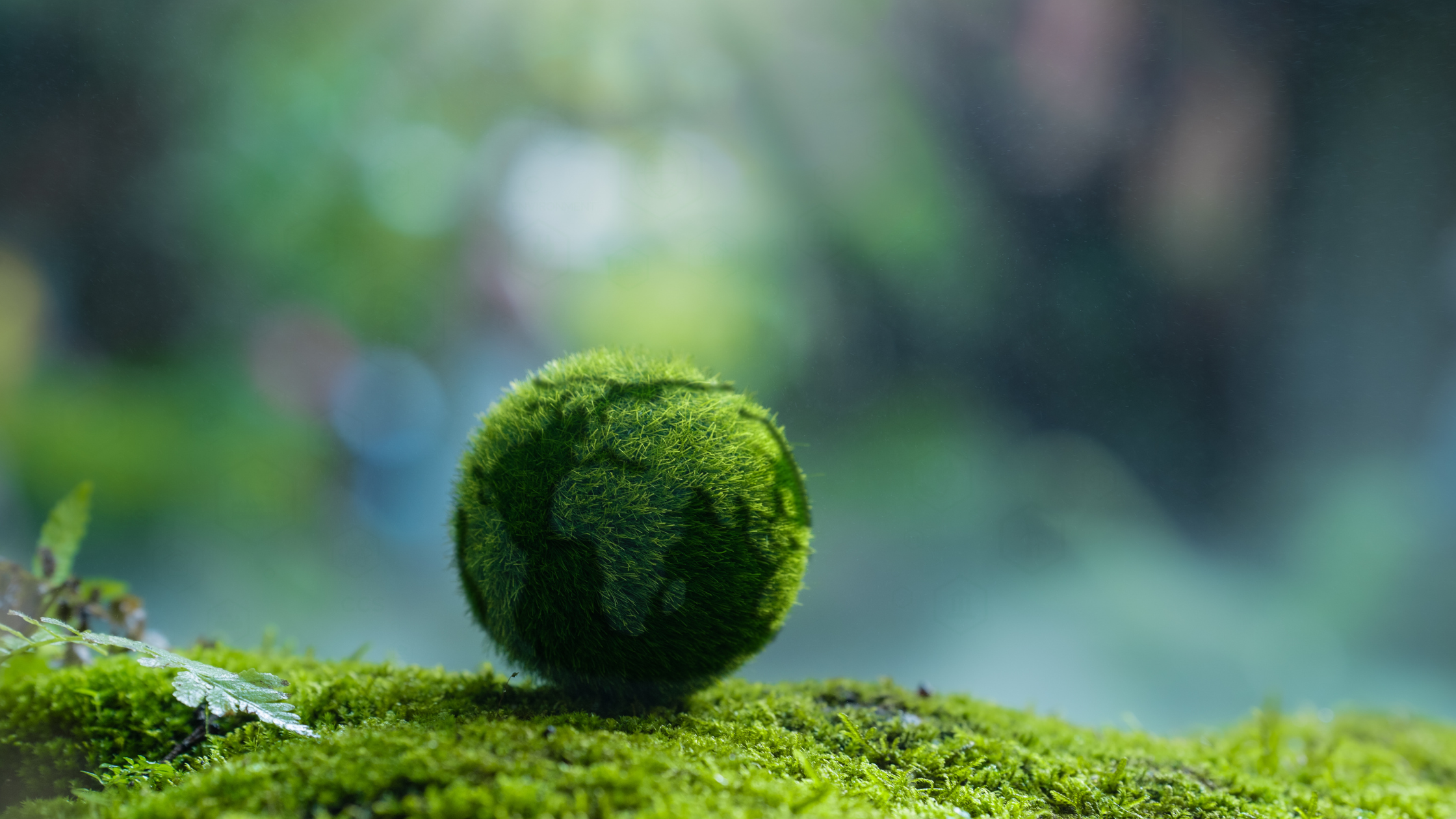
Metal Organic Frameworks (MOFs) & Organometallic Complexes for Carbon Capture and Storage Utilization
Carbon Capture Technologies
In the global effort to reduce greenhouse gas emissions, Carbon Capture and Storage (CCS) technologies have emerged as crucial tools. Advanced materials like Metal-Organic Frameworks (MOFs) and Organometallic Complexes are pivotal in improving CCS efficiency. These technologies help capture, store, and utilize CO₂ across a range of applications, from industrial processes to sustainable energy solutions.
Characteristic Features of MOFs for CCS Applications:
1. Industrial Processes:
a) Chemical manufacturing: Different industries like ammonia and hydrogen production emit CO2 during chemical reactions which can be captured via this CCS technique.
b) Steel production: During the process of steel making, large quantities of CO2 are being produced through the blast furnace route. The CCS technique can then mitigate the release CO2 emissions.
c) Cement production: One of the significant sources of CO2 emissions is the cement manufacturing process due to calcination of CO2. The CCS process can capture these emissions at the source.
d) Refineries: Oil refineries release CO2 during the processing of crude oil into various products which can be minimized by the CCS technique.
2. Power generation:
a) Fossil fuel power plants: CCS technique can be applied to coal, natural gas and oil-fired power plants in order to capture CO2 emissions during electricity generation.
b) Biomass power plants: The process of CCS results in negative emissions since biomass absorbs CO2 during its growth and storing the captured CO2 reduces the atmospheric CO2 levels.
3. Direct air capture (DAC):
a) Atmospheric CO2 removal: DAC technique captures CO2 directly from the ambient air. The captured CO2 can be then stored or utilized, contributing to CO2 removal Strategies.
4. Bioenergy with carbon capture and storage (BECCS):
ECCS technique involvescapturing CO2 from different bioenergy processes like fermentation or biomass combustion. During the growth process, CO2 is being absorbed by biomass whichresults in net negative emissions.
5. Enhanced oil recovery:
Oil field operations: Herein, the captured CO2 is injected into depleted oil fields in order to increase the amount of oil which can be extracted. Hence, this method stores CO2 underground, providing a dual benefit.
6. Natural gas processing:
Acid gas removal: CO2 is being removed during the processing of natural gas in order to meet the desired pipeline specifications. So, this CO2 is then captured and being stored instead of being vented to the atmosphere.
7. Waste-to-Energy:
Incineration of wastes: Several waste-to-energy plants burn municipal solid wastes which in turn release a lot of CO2 emissions into the atmosphere. So, by employing CCS technique, the generated emissions can be captured thereby minimizing the carbon footprint of waste management.
8. Hydrogen production:
Blue hydrogen: Hydrogen produced from natural gas using steam methane reforming (SMR) process generates CO2 as a by-product. This released CO2 is then captured by CCS technique, resulting in low-carbon hydrogen, known as “blue Hydrogen”.
9. Chemical recycling and utilization:
Carbon utilization: The CO2 being captured by CCS technique can be utilized as a raw material for the production of chemicals, fuels and materials like polymers, carbonates and synthetic fuels, thereby providing an alternative to traditional fossil- derived products.
10. Agriculture and forestry:
Soil carbon sequestration: Several practices that enhance carbon storage in soils (biochar applications) and forests (afforestation) are focused on increasing carbon Sinks.
11. Geothermal energy:
Several geothermal plants release CO2 naturally stored in underground reservoirs. The CCS technique is utilized then in capturing these
emissions, making geothermal energy cleaner. In some embodiments, the disclosure relates to the characteristic features of metal-organic frameworks (MOFs) that make them ideal for carbon capture and storage (CCS) applications:
High surface area: MOFs possess high surface area, thereby providing abundant sites for CO2 adsorption which allows them to capture large amounts of CO2 relative to their Weight.
Characteristics
1. Tuneable pore size and structure:
Customizable porosity: It is possible to control the pore size of the MOFs during their synthesis. This tunability allows for the design of MOFs with pore dimensions that are ideal for trapping CO2 molecules, thereby enhancing their selectivity and capability for CO2 capture.
2. Flexible frameworks:
Most of the MOFs with flexible frameworks can adapt their structure in response to the guest molecules, which can improve the efficiency of CO2 capture.
3. High CO2 selectivity:
a) Selective adsorption: MOFs can be designed in a way that they can preferentially adsorb CO2 over other gases like nitrogen (N2) or methane (CH4). This selectivity is essential for effective CO2 capture in various industrial applications.
b) Microporous structures: Most of the MOFs being microporous in nature are able to selectively capture small CO2 molecules while excluding larger or non-polar Molecules.
4. Chemical versatility:
Functionalization: Most importantly, it is possible to chemically modify the structure of the MOFs by encapsulating functional groups either into their metal nodes or organic linkers. One of the examples of such frameworks are the amine-functionalized MOFs which can strongly interact with CO2 through chemical bonding thereby increasing their capture efficiency. This functionalization enhances the interaction between CO2 and the MOF, thereby increasing the adsorption capacity and selectivity.
Diverse metal centres and linkers: A large number of organic linkers and metal ions can be utilized in MOFs which allows for the design of materials with required properties tailored to CO2 capture including enhanced adsorption energy or selectivity.
5. Reversibility and Regenerability:
a) Reversible adsorption: MOFs can be designed to capture and release CO2 reversibly, thereby enabling them to be regenerated and reused in multiple cycles. This characteristic feature allows them to be highly used for CSS applications wherein, the operational costs are being minimized as well as the associated energy requirements with CO2 capture.
b) Low heat of adsorption: The carbon capture and storage process are energy-efficient as the energy required to regenerate MOFs by releasing the captured CO2 is lower than that required for other adsorbents.
6. Open metal sites:
a) Unsaturated metal centres: The presence of the unsaturated metal centres in most of the MOFs aid in acting as the strong adsorption sites for CO2. These open metal sites build strong affinity with CO2 molecules, thereby resulting in higher adsorption capacity, especially under low-pressure conditions.
b) Resistance to degradation: The high stability of MOFs ensures that they can maintain their structural integrity as well as performance over many cycles of CO2 adsorption and desorption, making them vital for long-term use.
c) Stability under harsh conditions: MOFs being both chemically and thermally stable allows them to withstand the harsh conditions encountered in various industrial processes like in the presence of moisture, corrosive substances as well as high temperatures.
d) Potential for CO2 utilization: Most importantly, the MOFs exhibit catalytic properties which can be fully utilized in converting the captured CO2 into useful chemicals or fuels, integrating capture with utilization. Hence, the dual functionality displayed by the MOFs enhances the overall value proposition of MOFs in CCS technologies.
7. Scalability and Processability:
a) Bulk synthesis: MOFs can be synthesised using different scalable methods which is crucial for their potential utilization in large-scale industrial applications.
b) Processable forms: Lastly, the MOFs can be incorporated into various forms, such as pellets, membranes or composites which are ideal for different types of CO2 capture processes like gas separation, direct air capture etc.
MOFs exhibiting large surface areas and tuneable properties have significantly gained attraction for their potential in carbon capture and storage due to their ability to selectively capture and store CO2.
Herein, some aspects of the disclosure focus on how CCS technique can be utilized on particularly energy applications using these metal-organic frameworks:
Uses
1. Pre-combustion carbon capture:
a) High-pressure CO2 capture: Some of the MOFs can be typically designed to capture CO2 under the high-pressure conditions typical of pre-combustion processes, thereby providing a more efficient alternative to conventional solvents.
b) Syngas purification: MOFs can be effectively utilized in capturing CO2 from syngas before combustion in several Integrated Gasification Combined Cycle (IGCC) power plants. This enables for the production of a cleaner hydrogen-rich fuel and the subsequent storage of captured CO2.
2. Post-combustion capture:
Several MOFs can be utilized in capturing CO2 from various exhaust gases of power plants that burn fossil fuels such as coal and natural gas. The exhaust gas is then passed through a MOF-based filter wherein CO2 is being selectively adsorbed onto the MOF material.
3. Flue gas treatment:
CO2 is a major by-product being released by various fossil fuel- based power plants. MOFs possessing large surface areas and highly tunable structures are specifically being designed to capture CO2 from flue gases. This process involves passing the exhaust gases through MOF-filled columns where CO2 molecules are being adsorbed, leaving behind other gases like nitrogen or water-vapor.
4. Direct air capture:
At the same time, MOFs can be potentially employed in DAC systems to capture CO2 directly released into the atmosphere. As a result, net atmospheric carbon levels can be minimized and can be successfully integrated with renewable energy sources like wind and solar which can effectively offset intermittent generation by capturing and storing CO2 when excess energy is available.
5. Storage and utilization:
a) Geological storage: Once CO2 is being captured by MOFs, it can then be compressed and injected into various geological formations like depleted oil and gas fields or deep saline aquifers. Hence, this is an essential step in ensuring that captured CO2 is sequestered permanently, thereby preventing its release back into the atmosphere.
b) Enhanced oil recovery: The captured CO2 can be utilized in EOR applications, wherein the gas is injected into mature oil fields in order to increase the oil extraction. Hence, the captured CO2 is being effectively utilized and also contributes to energy production, thereby integrating CCS into a circular carbon economy.
6. Nuclear power plants:
MOFs can be used in different nuclear power plants to capture CO2 from being produced during auxiliary processes like combustion of fossil fuels used in backup power plants. This effectively helps in minimizing the carbon footprint of nuclear energy.
Bioenergy with carbon capture and storage:
a) CO2 capture from biomass combustion: MOFs can be used to capture CO2 generated during the combustion of biomass which is one of the significant applications as it can create a carbon-negative energy system, where more CO2 is being captured, stored and finally released, aiding to offset emissions from the other Sectors.
b) Integration with biogas plants: MOFs can be used in biogas plants in order to capture CO2 from the biogas, thereby improving the purity of methane used as fuel and hence, enabling the storage or utilization of captured CO2. Some aspects of the disclosure enclose how metal-organic frameworks can effectively utilize CCS technique and revolutionize the process of manufacturing by both capturing and storing CO2 as well as converting it into valuable feedstocks, thereby creating a more sustainable
Industrial ecosystem:
1. Pressure swing adsorption (PSA): Herein, the MOFs capture CO2 from flue gases at high pressure. When the pressure is lowered, CO2 is being released from the MOF allowing for its collection, storage and utilization.
2. Temperature swing adsorption (TSA): Herein, CO2 is being captured at lower temperatures by MOFs. Further, the temperature is increased to release the CO2 which can be stored and then converted into useful products.
3. CO2 curing of concrete: MOFs can capture CO2 from industrial processes, which is then utilized in the curing of concrete. During the process, CO2 reacts with calcium compounds in the concrete thereby resulting in the formation of calcium carbonate thereby enhancing the strength of the concrete.
4. MOF-enhanced carbonation: MOFs can be utilized in enhancing the process of carbonation in cement production, thereby capturing CO2 during manufacturing process and using it to improve the properties of the desired product. Thus, the technique can be utilized in capturing both CO2 as well as turning it into a useful component of the construction material, thereby providing a dual benefit of carbon sequestration and material enhancement.
5. Bioplastic production: MOFs can trap CO2 and then convert it into monomers for bioplastic production via catalytic processes wherein the MOF adsorbs CO2 and facilitates its reaction with other feedstocks to produce biopolymers. Hence, the CCS technique can be used as an alternative to traditional plastic production, minimizing the dependence on fossil fuels and lowering the carbon footprint of the manufacturing process.
6. Integration with renewable energy: MOFs can be effectively employed in several systems which use renewable energy to drive the conversion of captured CO2 into sustainable plastics, thereby creating a closed-loop manufacturing process.
Samples of Viva Bio family of MOFs which can be highly employed for CCS applications:
1. Zeolitic Imidazolate Frameworks (ZIFs): MOFs like ZIF-8, ZIF-67 based on imidazolate linkers can be effectively used for the process of carbon capture and storage due to their excellent thermal and chemical stability. These MOFs also show potential for CO2 capture due to their high surface area as well as high selectivity for CO2 over other gases.
2. Zr-based family of MOFs: MOFs built from the zirconium clusters (UiO-66, UiO-67) exhibit high stability under a wide range of conditions. These MOFs can further be modified or tuned with different functional groups (amine groups) in order to enhance CO2 adsorption capacity and selectivity.
3. MOF-74 Series (CPO-27): These MOFs (Mg, Zn, Ni, Co) exhibit high density of unsaturated metal sites which can strongly interact with CO2 molecules.
4. Amino-functionalized MOFs: The presence of amine groups into the framework (NH2-UiO-66, NH2-MIL-101) aids in forming stronger interactions with CO2 through chemisorption, hence enhancing the overall capture capacity even at low pressures.
5. MIL Series (Materials of Institute Lavoisier): MIL MOFs such as MIL-53, MIL-100, MIL-101 with large pore sizes, functionalizable cavities and high surface areas are known to adsorb significant amounts of CO2.
6. MOFs with mixed linkers: The incorporation of multiple linkers (mixed ligand MIL- 101) or post-synthetic modification allows for tuning of pore size, functionality and affinity for CO2 which allows for optimizing these MOFs especially for CCS Applications.